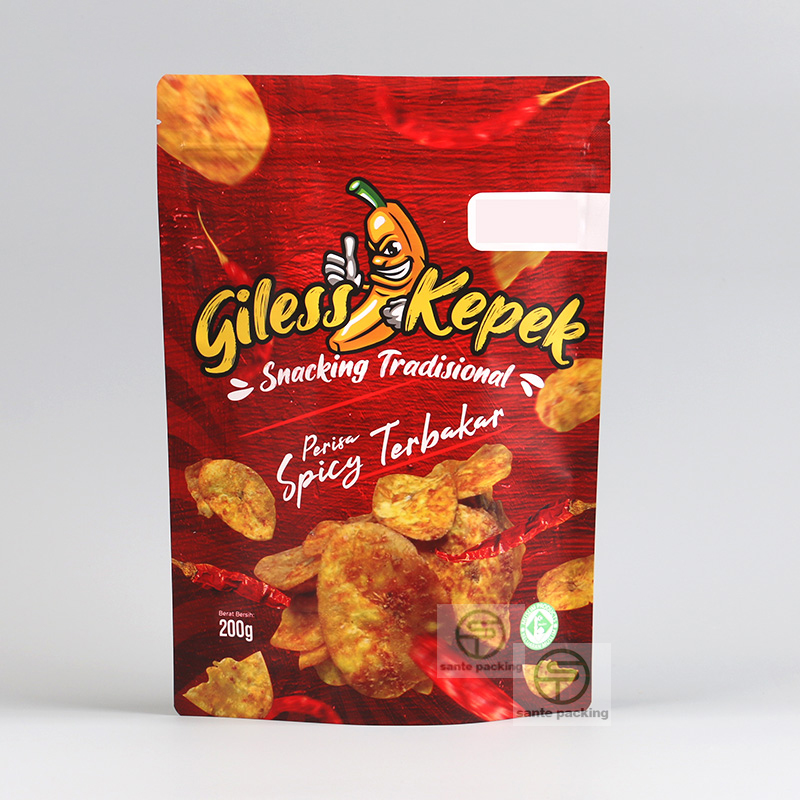
A stand-up pouch is a versatile and flexible packaging solution designed to stand upright on its bottom, making it ideal for product display, storage, and easy usage. This comprehensive guide will walk you through the entire SantePack stand-up pouch manufacturing process, covering every essential stage from initial planning to final quality testing.
1. Determine the Purpose of the Stand-Up Pouch
- The first and foremost step in manufacturing a stand-up pouch is to clearly define its specific purpose. Whether the pouch is intended for preserving freshness, protecting the product, or simply storing it, understanding its purpose is critical.
- Once the purpose is determined, it becomes easier to choose the appropriate materials, design, size, and shape that will best meet the needs of the product it will contain.
- For instance, if the pouch is to be used for packaging food or beverages, selecting materials that ensure the safety and freshness of the contents is crucial. This step helps in laying the foundation for all subsequent decisions in the manufacturing process.
2. Design Process
- After establishing the purpose of the stand-up pouch, the next step is to engage in the design process. This involves using specialized design software to create a conceptual model of the pouch.
- The design phase is complex and requires a deep understanding of how to use the software to produce a design that meets both functional and aesthetic needs.
- During this stage, several factors need to be considered, including the type of content, the target market, and the overall functionality of the pouch. For example, you might need to decide whether to include features like ziplocks, spouts, press-to-close seals, or tear notches, depending on the content the pouch will hold.
- Additionally, the design should take into account customer preferences and market trends, ensuring that the pouch not only serves its functional purpose but also appeals to the consumer. Customizing the design to suit specific customer requirements can also help differentiate your product in a competitive market.
- Another important aspect of the design process is estimating the overall cost and potential return on investment. By considering these factors early on, you can make informed decisions that balance quality with cost-effectiveness.
3. Selecting the Right Material
- The choice of material is a critical component in the manufacturing of stand-up pouches, as it directly affects the practicality, durability, and efficiency of the final product.
- Typically, a stand-up pouch consists of three layers: the inner layer, the middle layer, and the outer layer, each serving a specific purpose. These layers are laminated together to form a cohesive and functional pouch.
- Inner Layer: The inner layer is in direct contact with the product and is often made from materials like linear low-density polyethylene (LLDPE). This material is FDA-approved for food contact, provides excellent heat-sealing properties, and ensures the product is tamper-proof, thereby extending shelf life and boosting consumer confidence.
- Middle Layer: The middle layer varies depending on the product’s requirements. Common materials include metalized film, aluminum foil, and polyethylene terephthalate (PET). Each material offers unique benefits, such as durability, barrier protection, and strength. For example, aluminum foil is ideal for products requiring a longer shelf life, while metalized film is suitable for products with a faster turnover.
- Outer Layer: The outer layer is the visible part of the pouch and plays a significant role in brand messaging and consumer attraction. Kraft paper is often used for its natural, eco-friendly appeal, enhancing the aesthetic and environmental value of the pouch. This layer also provides durability, strength, and protection against external elements.
4. Choosing the Suitable Design
- Selecting the appropriate design for a stand-up pouch is closely linked to the type of product it will contain and the preferences of the target market.
- The design should be functional, easy to use, and visually appealing to stand out on crowded retail shelves. For instance, if the product is a liquid or semi-liquid, a pouch with a spout or cap would be more practical, allowing consumers to easily pour and reseal the contents.
- Customization is key in this stage. The pouch should be tailored to meet the specific needs of your target customers, whether it involves unique shapes, sizes, or additional features like euro slots for hanging displays. A well-designed stand-up pouch not only protects the product but also enhances the consumer’s experience by making the product easy to access, use, and store.
- Additionally, incorporating resealable features like ziplocks or press-to-close seals ensures that the product remains fresh even after opening, adding to the pouch’s functionality and consumer appeal.
5. Manufacturing the Stand-Up Pouch
- The manufacturing process of a stand-up pouch involves several intricate steps. It starts with the raw materials being passed through sets of plows that shape the material into W-shaped gussets, which are crucial for the pouch to stand upright.
- If the pouch requires a zipper, it is sealed onto the inner surfaces of the material near the top edge early in the process. Other access methods, such as perforations, spouts, or tear notches, are also added at this stage, depending on the design.
- Vertical seals are then created along the sides of the pouch, and the bottom folds are cut and sealed to form the main container part of the pouch. The final shape of the pouch is achieved by cutting it apart vertically through the center of the side seals.
- Once the pouch is formed, it is filled with the product, after which the top seal is applied, and the ziplock is closed. A notch is typically added near the top to facilitate easy opening by the consumer.
6. Quality Testing
- Ensuring that each stand-up pouch meets the required quality standards is vital. This is achieved through a series of rigorous tests designed to assess the pouch’s durability, functionality, and safety.
- Tensile Test: This test evaluates the material’s strength and how much it can stretch before breaking.
- Drop Test: This test determines the height from which the pouch can be dropped without sustaining damage, ensuring it can withstand handling during shipping and storage.
- Burst Test: This measures the maximum pressure the pouch can endure before bursting, which is crucial for products that may expand under certain conditions.
- Seal Strength Test: This assesses how well the seals hold up over time, ensuring that the contents remain secure and uncontaminated.
- Vacuum Test: This test checks for any potential leaks when the pouch is subjected to vacuum pressure, ensuring the integrity of the packaging.
- Bypassing these tests, the stand-up pouches demonstrate their reliability and suitability for a wide range of products, guaranteeing that they meet the highest standards of safety and quality.
In conclusion, the SantePack stand-up pouch manufacturing process is a meticulously planned and executed operation that ensures each pouch is crafted to perfection. From determining the purpose of the pouch to selecting the right materials and design, and finally ensuring that the product meets all quality standards, every step is designed to produce a pouch that not only meets but exceeds consumer expectations.
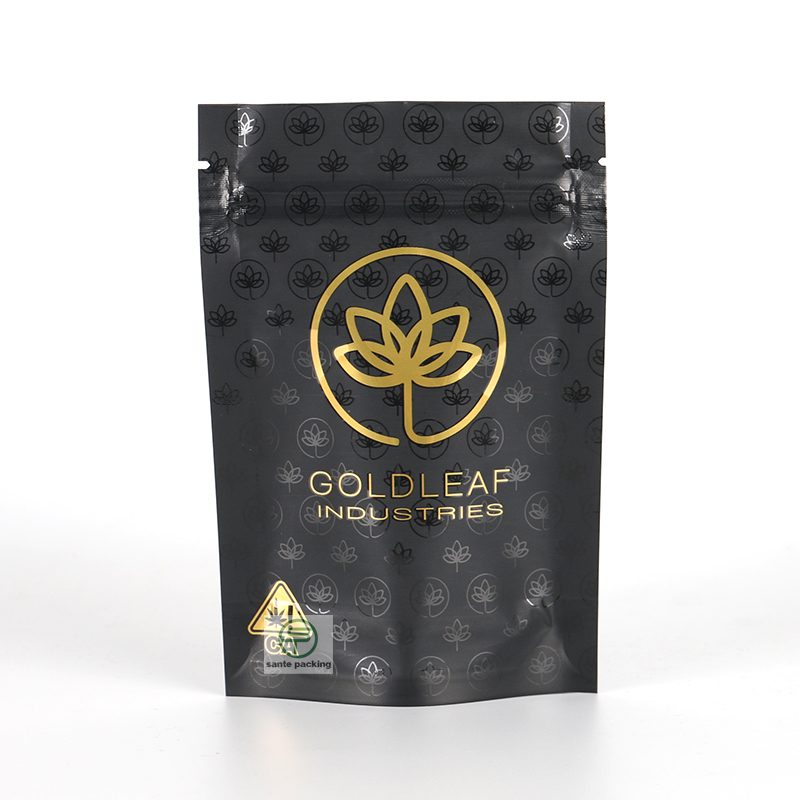